WDW in Maassluis is a wholesaler for sandwich panels, sheet piling, flashing and mounting materials. Thanks to a large stock of sandwich panels, the required materials can be supplied quickly and tailor-made for projects such as a new facade or partition wall, a roof renovation or making a home more sustainable.
Faithful bench
This is possible thanks to our own bending machine, on which flat sheet material is bent into certain positions. Flashing is used to finish the edges, corners and sides of roofs, facades and walls.
In the workshop WDW access to an old folding bench. This was built in 1991 and was operational for many years at a Belgian sandwich manufacturer. The machine has been in use at WDW for quite some time. He is used daily to realize typesetting for customers, both private and business customers. The flashings are used to finish sandwich panels in the desired color and coating, for example at the corners as well as at the top and bottom. The most common material used is 0.63mm steel, but aluminum and Sendzimir in different thicknesses are also no problem. Aluminum can be set up to a maximum of 3 mm thick and sendzimir up to 2 mm thick.
Bumpy months
But WDW has had a few bumpy months, in which the loyal beneficiary let employees down a number of times. There was wear and tear on various moving parts (hydraulics) and there were malfunctions in the electronics. “Every time one part was replaced, a new challenge arose with the subsequent – now outdated – part,” says Ilona de Ligt. “Due to the outdated software in combination with the high costs for individual parts, we ultimately took the plunge and decided on a complete overhaul.”
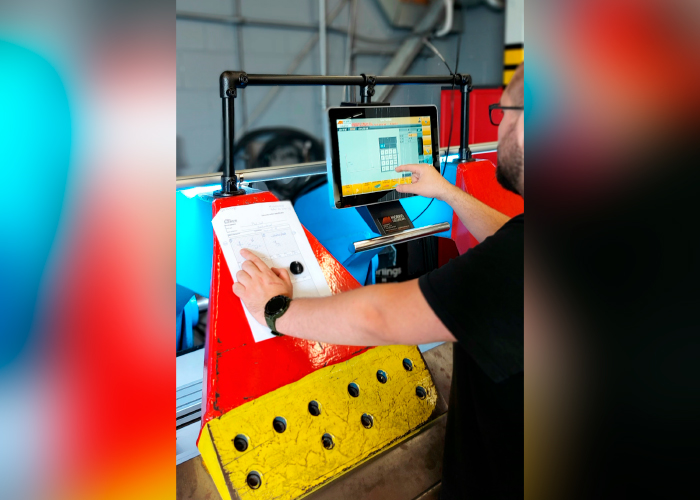
The efficiency mainly comes from the custom-made software – where standard/common typesetting is pre-programmed in the software.
Special control
This was realized by Morris Solutions, which overhauled the bending machine, including the steering and hydraulics. Not only various parts have been replaced. A completely new operating system has also been installed. Thanks to its specialist knowledge in this area, Morris Solutions was able to provide a control system that was specially developed based on the needs of WDW.
WDW is very satisfied with the progress of the work and even more so with the result. Ilona de Ligt: “The mechanical overhaul ensures that we can serve our customers again. The new control enables us to deliver high-quality brewing weeks with an accuracy of 0.5 mm.”
Typesetting pre-programmed
She even calls the result astonishing, very shortly after the revision: “Not only do we work much more efficiently thanks to the new software. The efficiency mainly comes from the custom-made software – where standard/common typesetting is pre-programmed in the software. The machine is also very accurate. Typesetting works are already very accurate during the configuration period. This is expected to only improve in the coming weeks, when people and machines have to become attuned to each other.”
The total overhaul by Morris Solutions has turned out to be a good choice: “We are extremely happy with it. Especially because after a difficult period in which the folding machine let us down a number of times, we can once again provide our loyal customers with high-quality custom folding work as usual.”
Morris Solutions is an exhibitor at METAVAK.
Morris Solutions
Stand E134