Nardo Machines and Services presents its own brand Benchmark Fiberlaser laser cutting machines at METAVAK. These are attractively priced, compact lasers for workshops where space is limited and where cutting is not done all day long.
Peter Plomp, owner of Nardo, introduced these lasers at the end of last year. He saw a gap in the market for compact machines and he was right. He sold the first copy at the end of 2022 and the counter now stands at twelve, of which ten have already been installed.
Sliding table
The Benchmark Fiberlaser machines are compact, have high-quality components and are equipped with an IPG laser source. They do not have a changing table, but a sliding table. This makes them compact and also makes attractive pricing possible. The machines are available in different sizes. The best-selling one is the one with a working range of 3×1.5 meters, the most common size in the metalworking industry.
“With the Benchmark Fiberlaser machines, we focus on companies with smaller workshops, who do not work 40 hours a week and are looking for an affordable machine that does not take up too much space,” says Peter Plomp. “They are available with sources from 1 kW to 6 kW. That is more than sufficient for this type. For customers who need more power and really want to run production, we have Yawei machines in our range. But they have a changing table and for that you quickly need a space of 10×5 meters.”
Nardo does the maintenance and service itself and together with a partner. “We have a total of 4 to 5 people who can do maintenance. We have parts in stock and there is always a model in our showroom in Hendrik-Ido-Ambacht. This way we can act very quickly if something is wrong. But so far we have had little to no problems. The customers are very satisfied.”
De Groot Luchtkanaal
One of those customers is De Groot Luchtkanaal in Weesp, specialist in the production, construction, supply and installation of air ducts and accessories. This company, which is particularly strong in the renovation market due to its flexibility, short lines and years of experience, has said goodbye to the ‘old’ plasma cutting table and started using the new laser. According to director Ron Zwagerman, the main reason for this was that plasma cutting produced a lot of particulate matter in the factory. “With a laser you have zero particulate matter. With this investment, we mainly looked at a healthy workplace for our employees.”
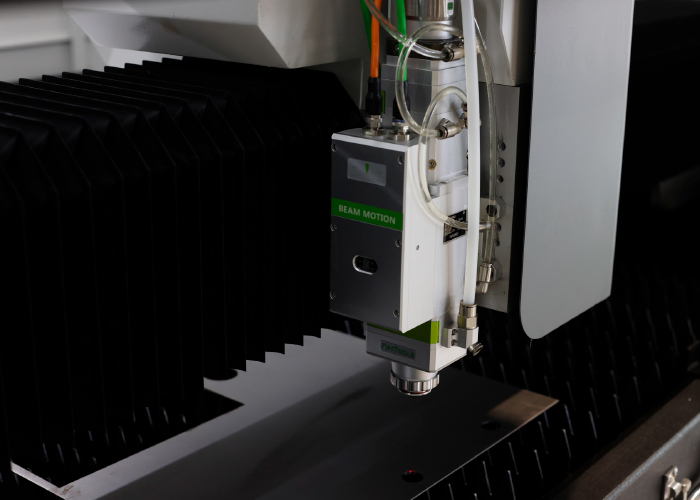
The laser cuts accurately to the hundredth of a millimeter.
But that is not the only advantage of the laser. According to Sander Swankhuizen, who heads the workshop, De Groot has improved enormously in several respects with the arrival of the laser. “The biggest advantage is indeed that you get rid of the material. But our products now also go out much better. The laser cuts accurately to the hundredth of a millimeter. That was unthinkable with plasma. The cuts are clean, there is no longer any rust on the plates, we have gotten rid of the orange deposits associated with plasma, we no longer have a blue flame in the workshop. And because the cutting edges no longer show hardening, our finishing machines last longer.
We are very satisfied with the end result.” Zwagerman adds: “We can now also make clean channels for use in hospitals and cleanrooms. These channels must be laser cut, this is not allowed with plasma.” The machine is also very user-friendly. “It obviously took some getting used to because we have always cut with plasma, if only because you now have a machine with a casing,” says Swankhuizen. “To be honest, I expected it to be more complex.”
Cutting production time quadrupled
The laser is in use daily. Swankhuizen estimates the pure cutting time at an hour per day. “Our cutting production time has quadrupled. That’s pretty decent. The plasma cutting table took up to 45 minutes to cut some small parts from a sheet. We now do that within 6 minutes. That contributes positively to our flexibility.”
A laser cutting machine was not interesting for De Groot for a long time because of the high costs. But nowadays there are lasers on the market that are cost-effectively feasible. Zwagerman: “The cost difference between plasma and laser has become much smaller. Considering the benefits, this laser is definitely worth the money. We are happy with this purchase.”
Nardo Machines and Services
Stand D130