[ad_1]
Driveway Downside
A tarmacked north going through drive, particularly with a skinny skim of outdated asphalt that slopes in the direction of the home, is at all times going to be a upkeep headache. Moss from the roof will get dropped onto the blacktop adopted by rain which by no means actually evaporates making an excellent haven for moss and algae to thrive turning the driveway right into a slippery and sludgy goo. Additional time this concoction eats away on the asphalt till it turns into only a muddy lavatory.

Driveway Resolution
In our case the reply was to exchange the tarmacadam and the backyard space with granite setts laid on a sand and cement base and infill with a structural grout that may forestall any weeds or moss from rising by means of or taking maintain. This development would even be straightforward to jetwash making the simply laid look of the cobles straightforward to take care of on an ongoing foundation.
Certificates of Lawful Growth
With the driveway being fairly a big space over 5 sq. metres I didn’t wish to take an opportunity with it falling foul of constructing laws so I submitted an software for a Certificates of Lawful Growth. Technically with the slope of the drive operating down in the direction of the property and not one of the rainwater runoff flowing off the property it didn’t require planning or constructing management approval.
As a result of there can be no absorption of the rainwater by means of the cobble stones a necessity will exist to put in a soakaway fed from a channel drain operating throughout the bottom a part of the drive.
I drew up plans and did some 3D drawings to assist the request for a Certificates of Lawful Growth and submitted the appliance which was duly ratified and issued by East Herts Distract Council.
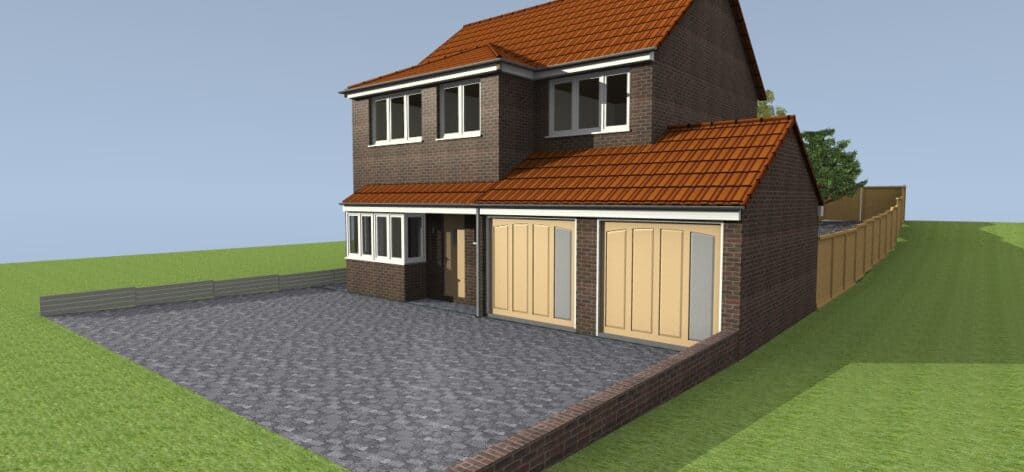
Materials Choice and Acquisition
I picked an untumbled granite cobblestone sett which might be grouted with Larsen Gunnable Pointing Mortar. Ten tonnes of the setts had been ordered and delivered together with thirty-five 25kg luggage of the Larsen GPM. A darkish gray engineered paviour was chosen as a border brick and 250 of those had been bought.
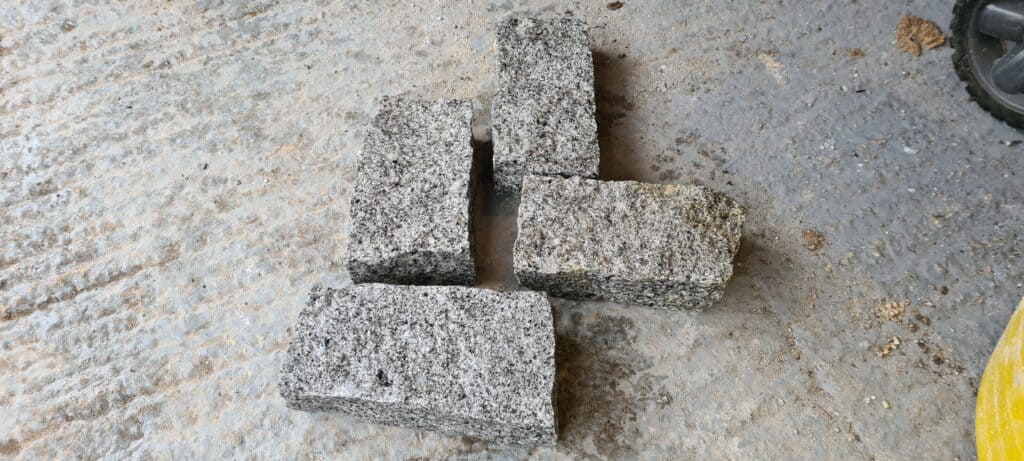
9 low voltage drive over floor lights and driver had been bought together with 9 Wiska junction containers and Raytech gel containers plus 50 metres of UV steady versatile exterior cable. To guard the cable operating underground I bought 50 metres of versatile conduit and screw in connectors. Armoured cable, glands, climate proof field and an exterior climate proof socket had been additionally bought.
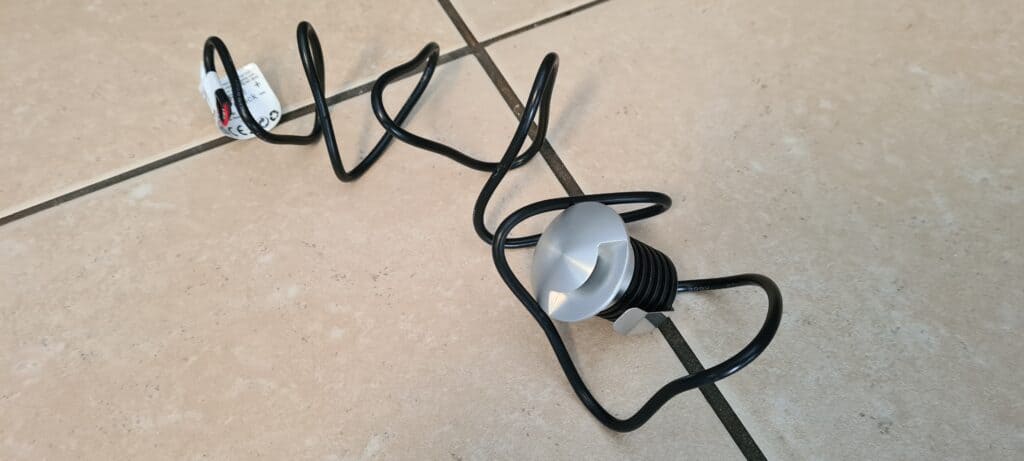
A flat-packed 1.5m2 soakaway was ordered together with 12 metres of channel drain together with a sump to permit the prevention of detritus from stepping into the soakaway. I additionally ordered 110mm pipe, sufficient to run from the sump to the soakaway together with double sockets, 15, 30 and 45 diploma bends to cater for the autumn that may be required to placed on the pipe from the sump to the soakaway.
6 tones of Ministry of Transport Kind One subbase was delivered together with 8 tonnes of sand and 16 luggage of cement.
The cobblestone setts had been delivered in a single tonne crates a number of weeks earlier than work was because of start so we handballed three of the crates spherical to the again of the home to create as a lot room on the drive as potential. I knew that we’d be shifting the setts across the drive on an ongoing foundation through the works as required.
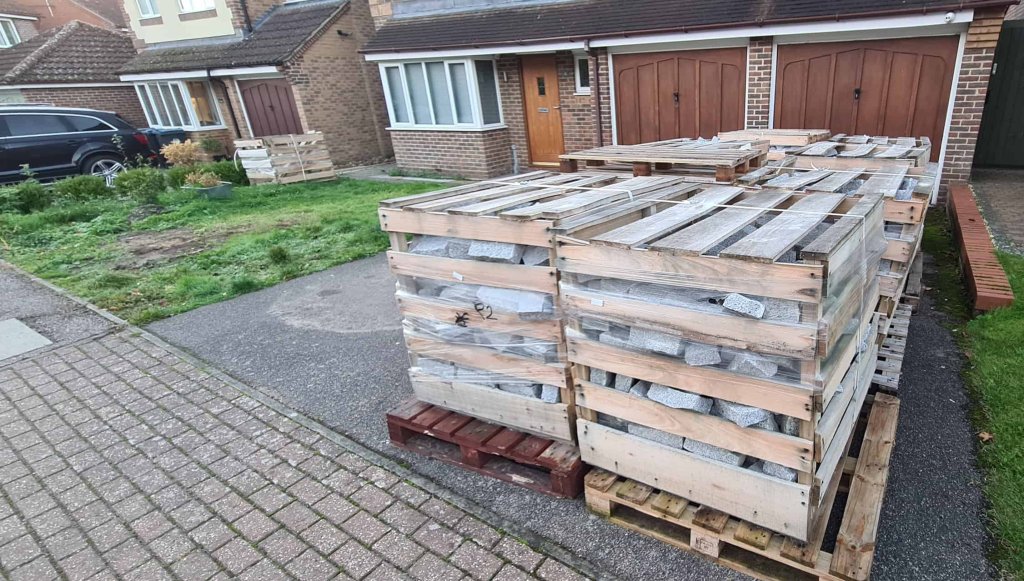
Floor Breaking Day
With all of the supplies in place the day arrived after we had been to begin work. The primary job was to drag up the present patio slabs and bushes that bordered the boundary fence. Foremost contractor Mark Winfield of M Winfield Constructing Companies took supply of the employed mini excavator. Utilizing the mini digger Mark began to tug top-soil off the positioning to be able to begin getting down in the direction of the eventual depth required to put down the MoT Kind 1 and sand and cement combine plus the cobble.
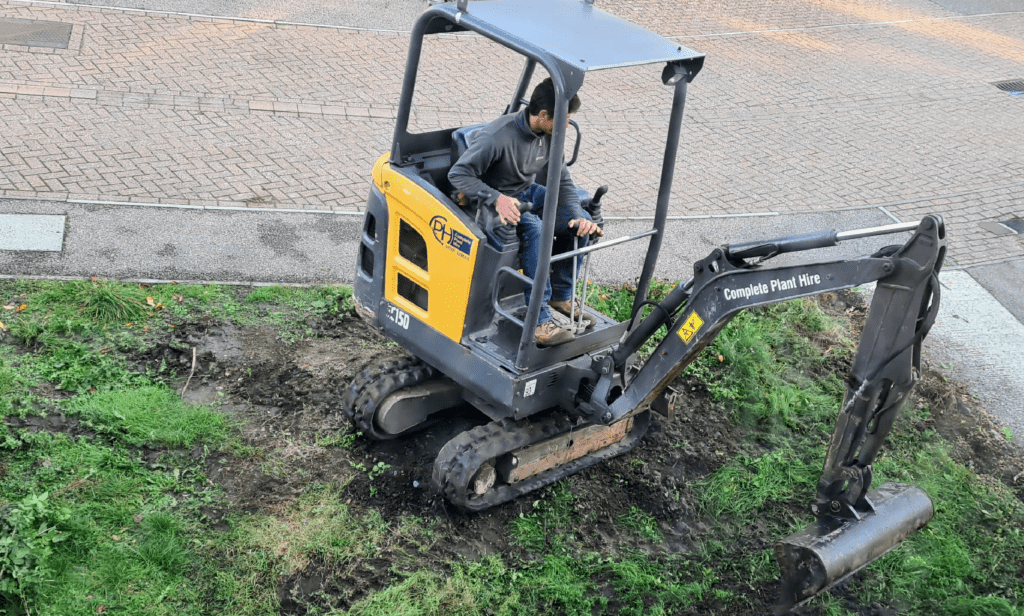
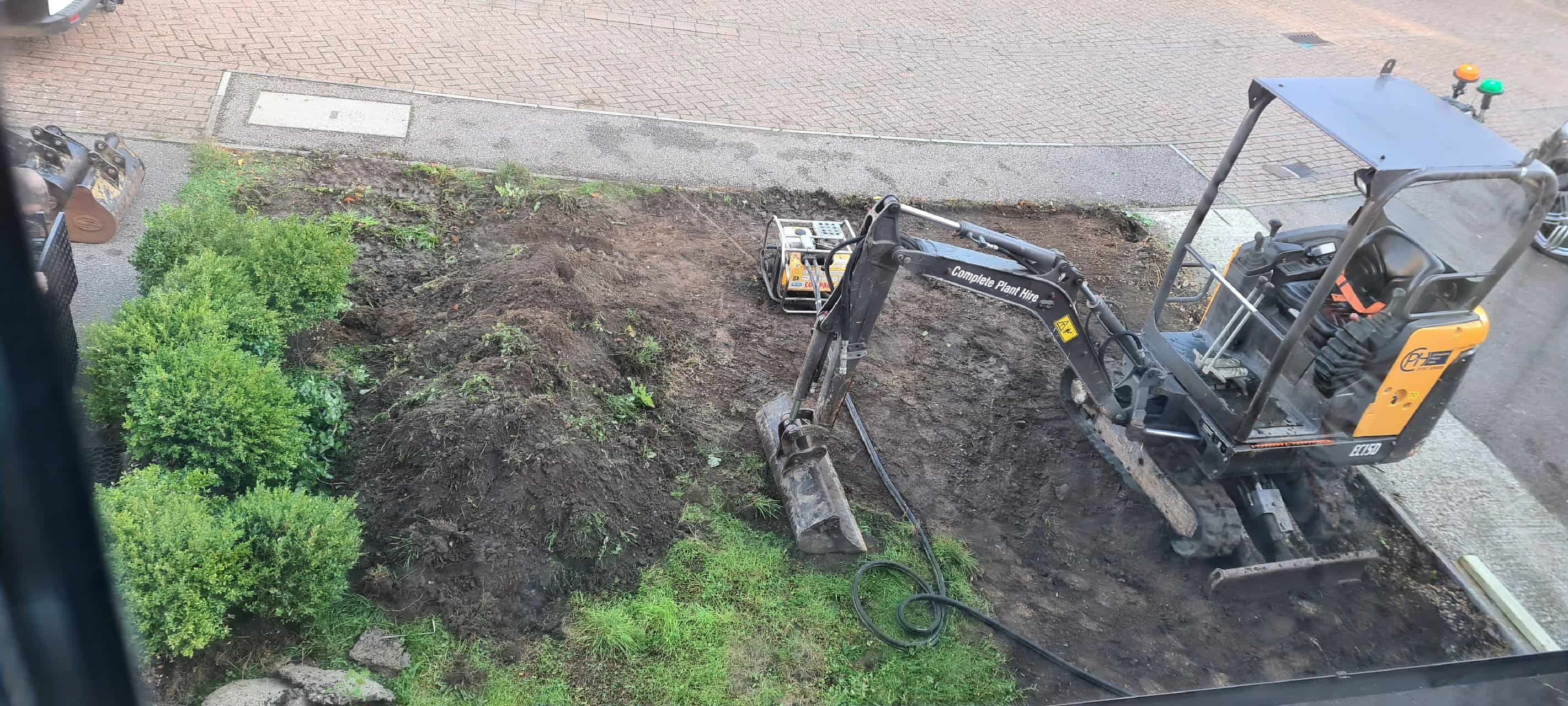
Breakers and Jackhammers had been used to bust out sporadic occurrences of concrete buried within the subbase. The digger was used to dig a trench within the required place from subsequent to the bay window to the place of the soakaway. Then the place of the soakaway was marked out and dug out with the mini digger. Sadly we hit the foundations of the outdated cinema that was there on the positioning earlier than the homes had been constructed so we needed to make the soakaway pit horizontal as an alternative of vertical.
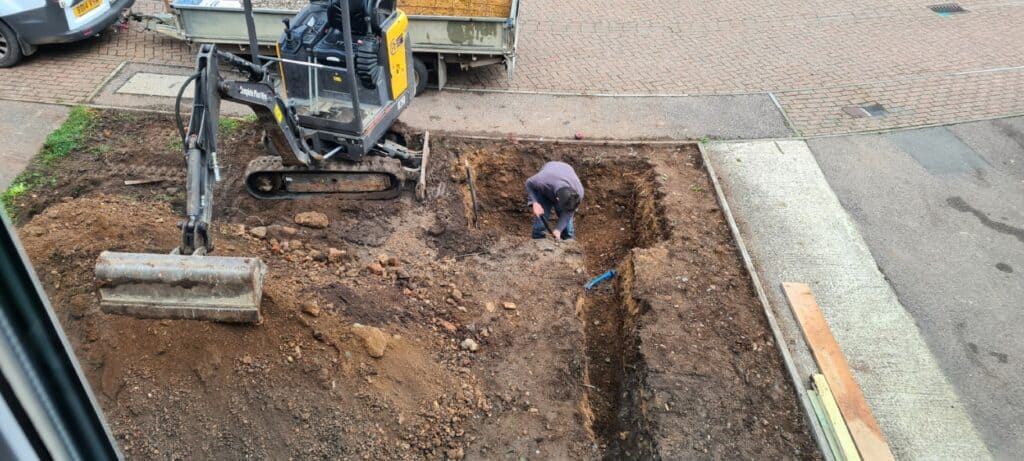
Soakaway Set up
Whereas digging the soakaway pit we got here throughout the water predominant which had been run diagonally throughout the backyard and with no warning tape or sand and shingle again fill to offer us a touch in regards to the place of the water predominant. The bucket of the digger went by means of the primary and I needed to make good with a brand new piece of blue pipe and connectors.
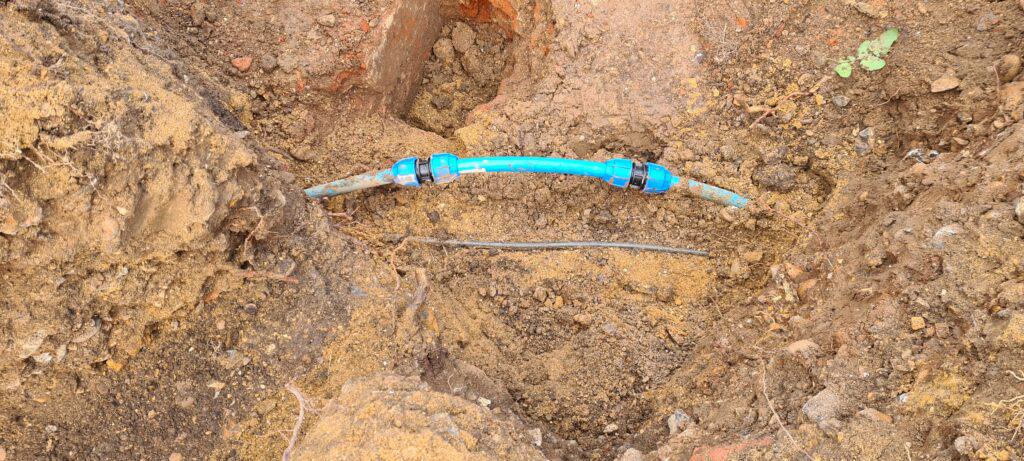
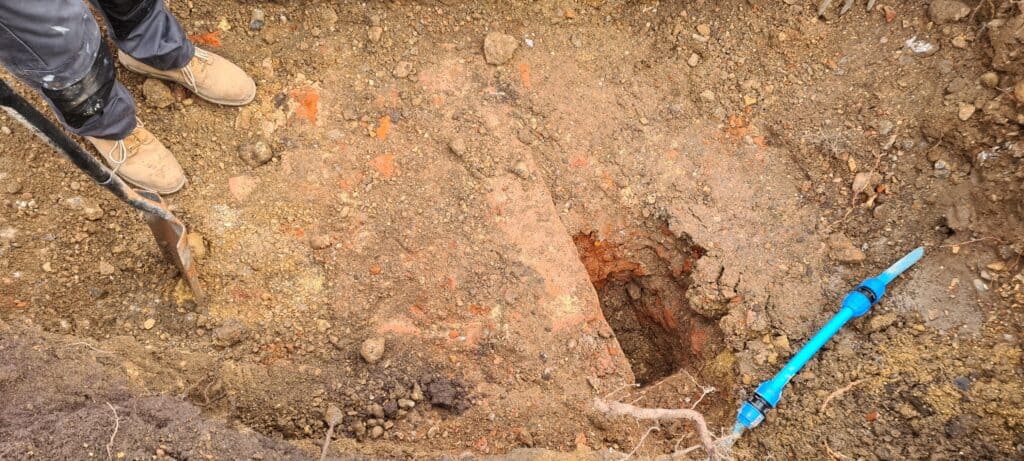
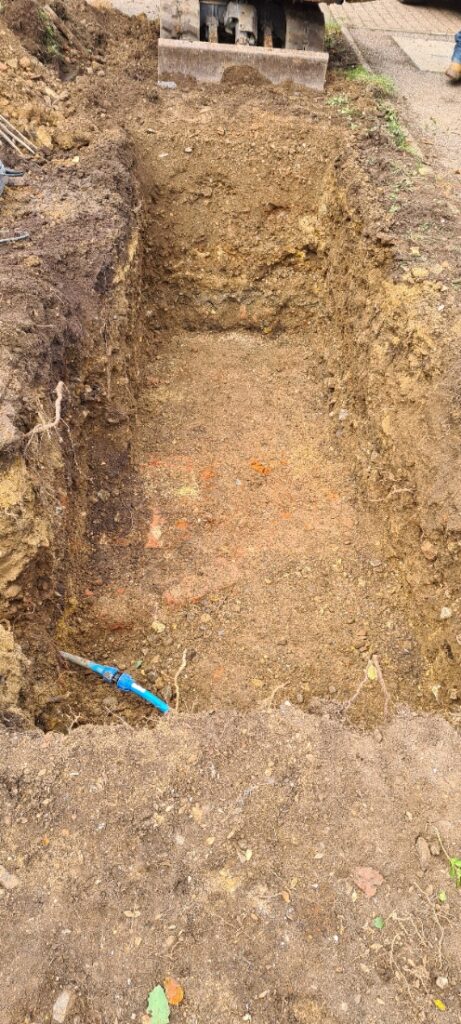
As soon as the pit was dug we infilled with shingle after which made up the soakaway creates and put in with membrane or terram. The 110mm pipe was then put in with the proper fall and fitted to the channel drain sump. Then we backfilled the soakaway pit with sand and shingle and coated with concrete.
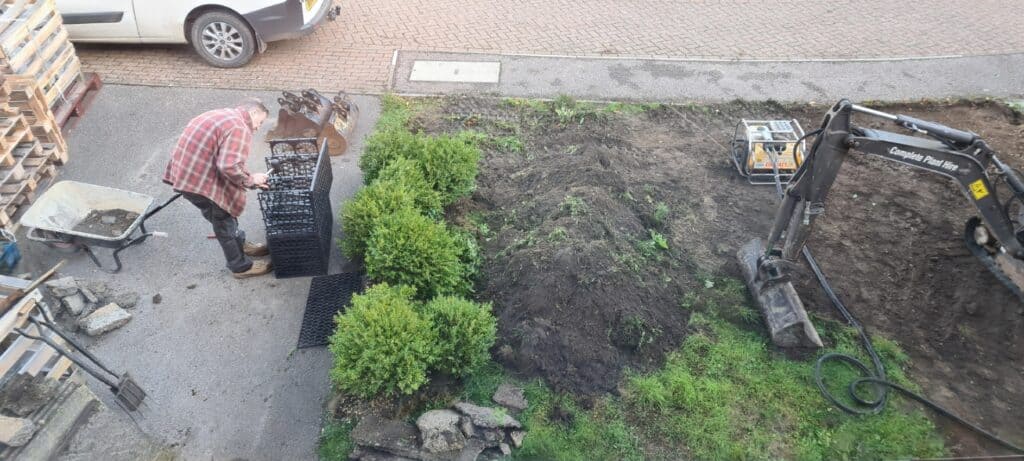
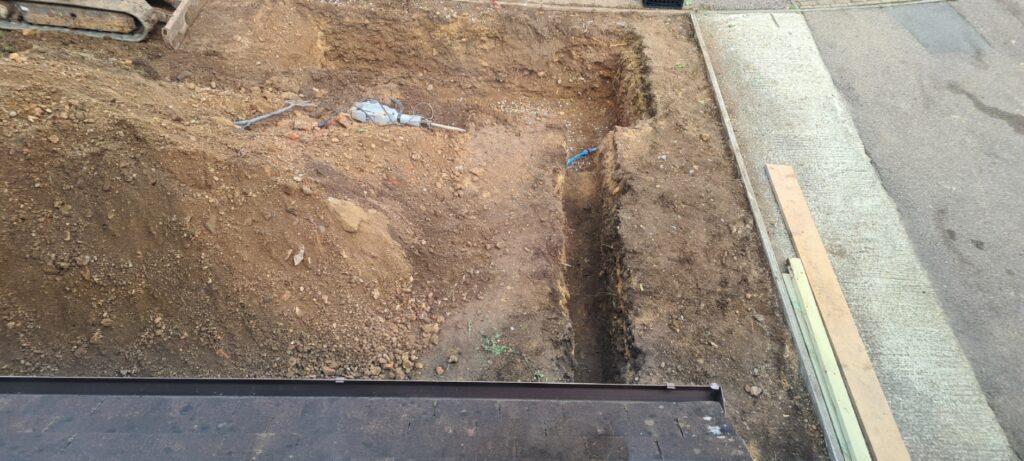
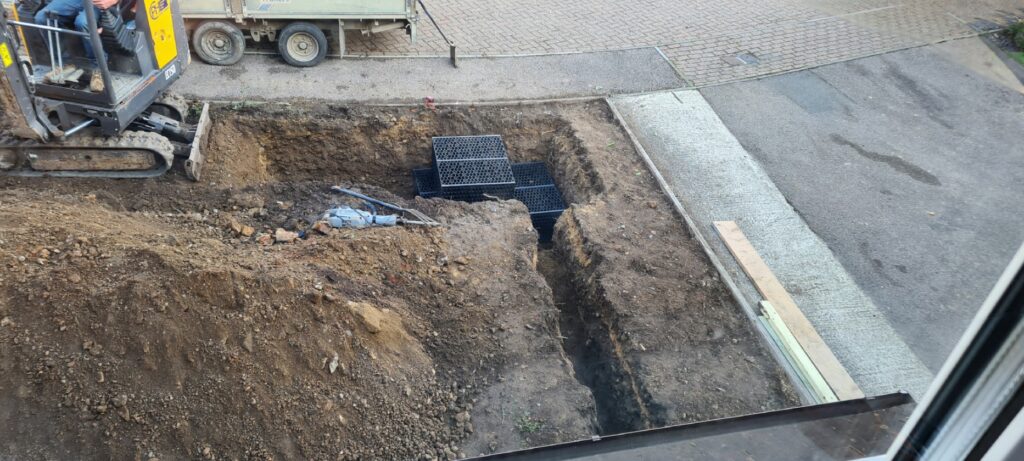
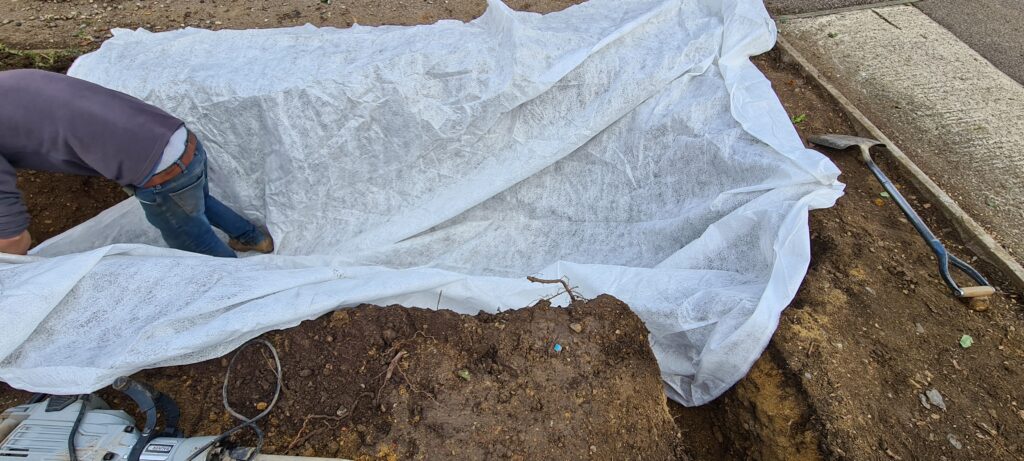
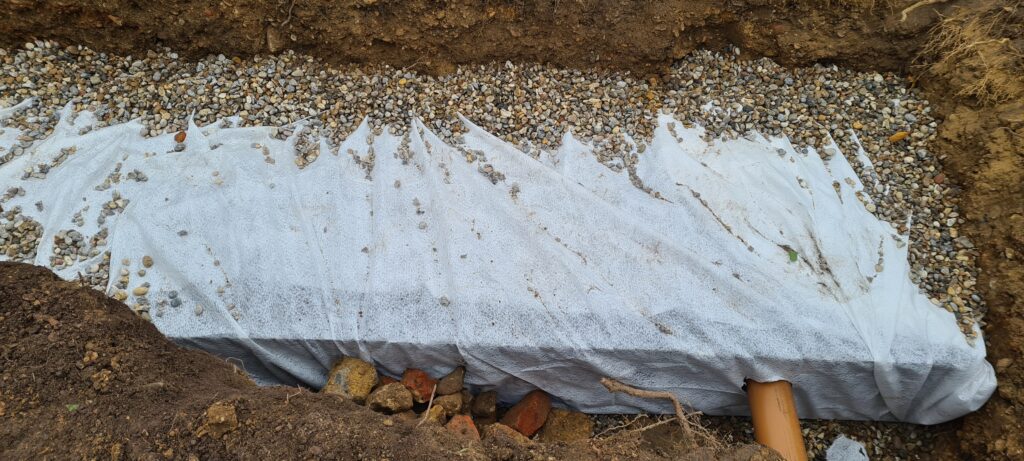
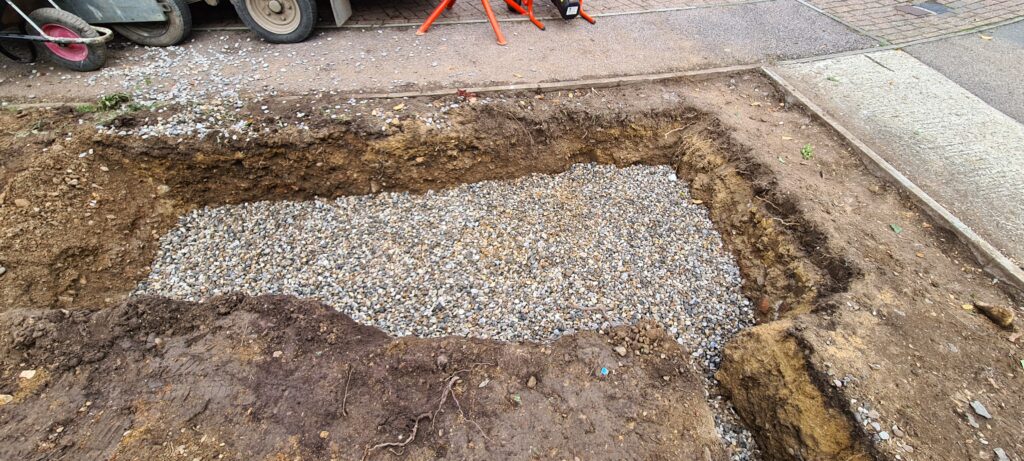
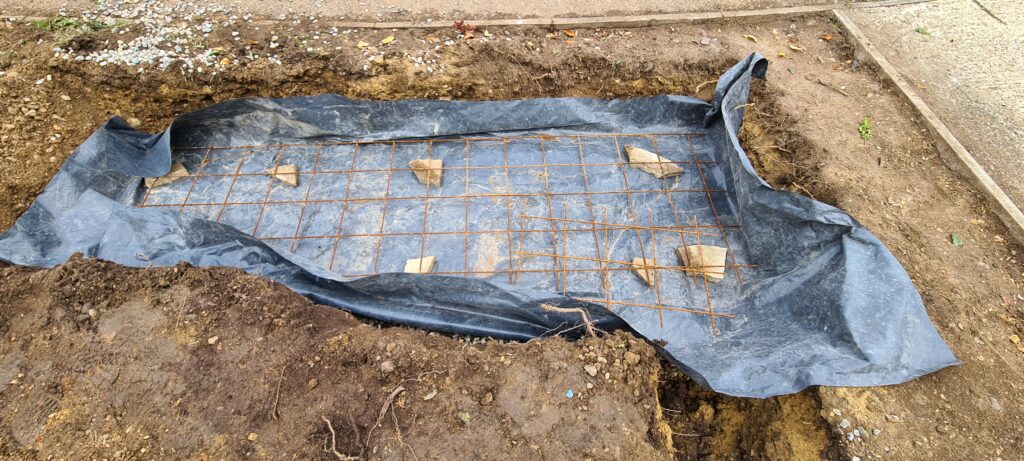
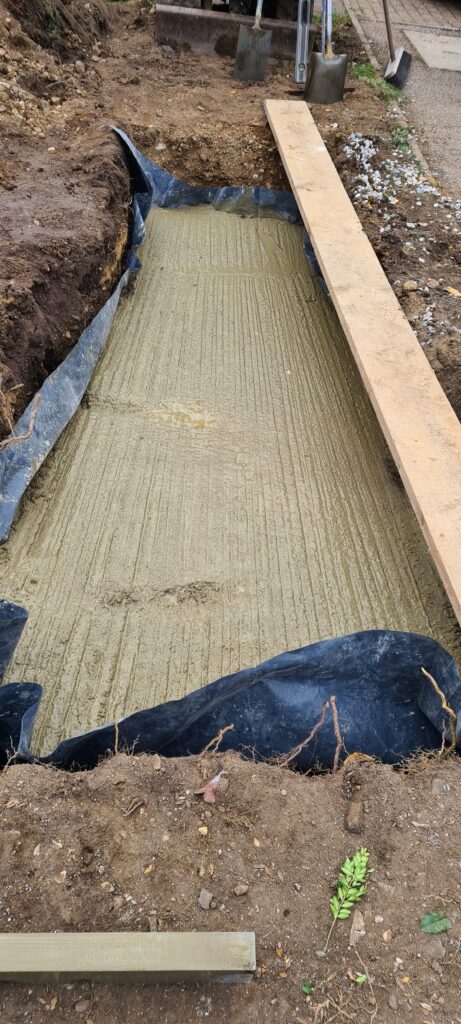
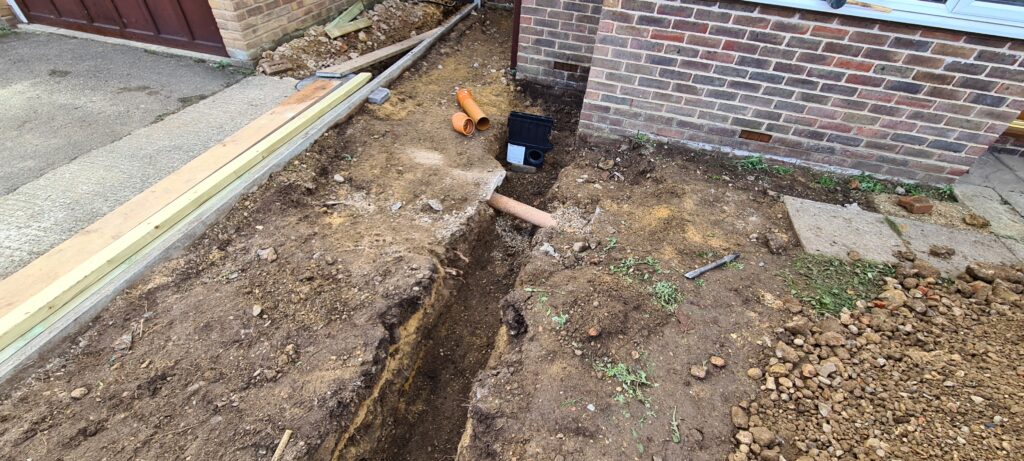
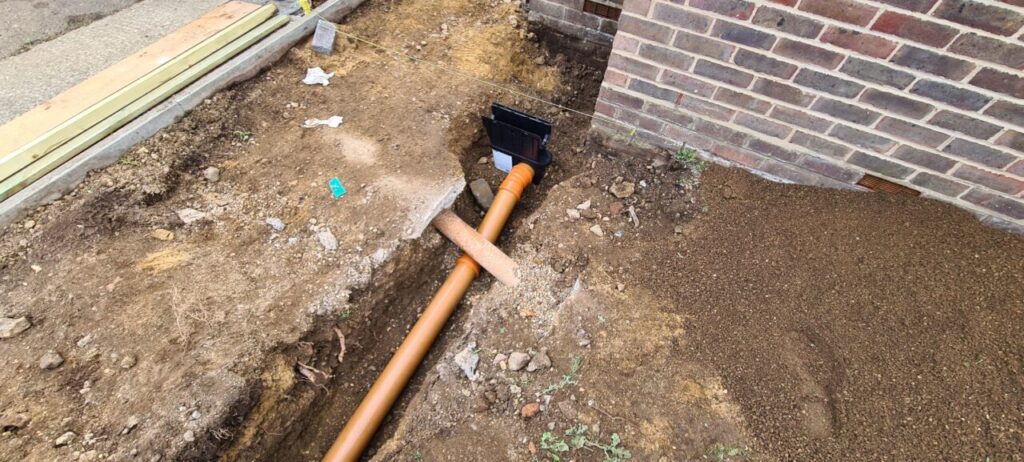
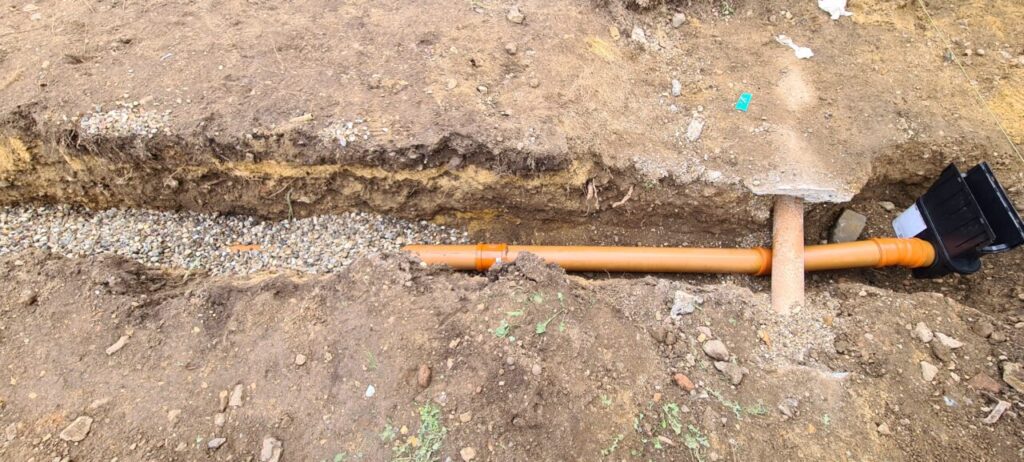
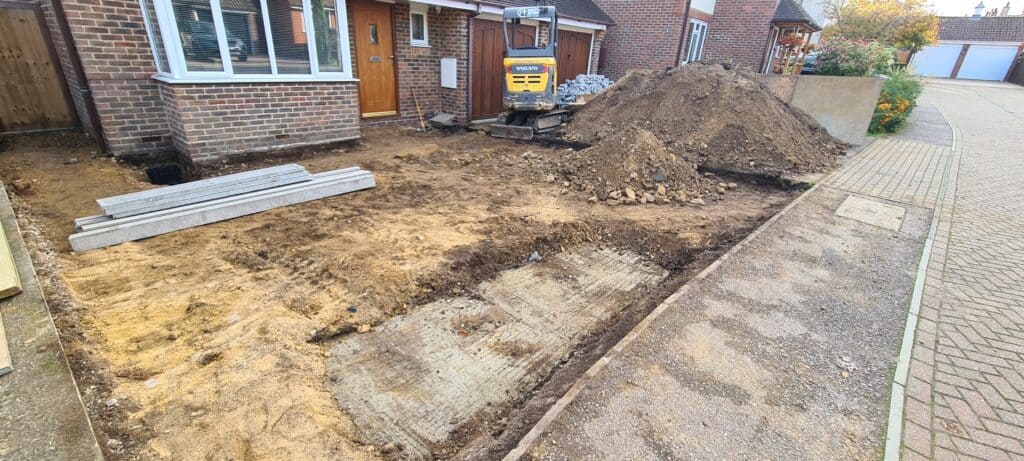

Earth Transferring and Web site Levelling
Now the soakaway was put in and concreted within the technique of pulling a degree with a string line and grading the positioning continued. This began by shifting the mound of spoil already amassed in a single place to a different pile over on the driveway. We additionally handballed the cobble setts within the crates on the drive out of the crates and right into a pile in a single place and removed the crates.
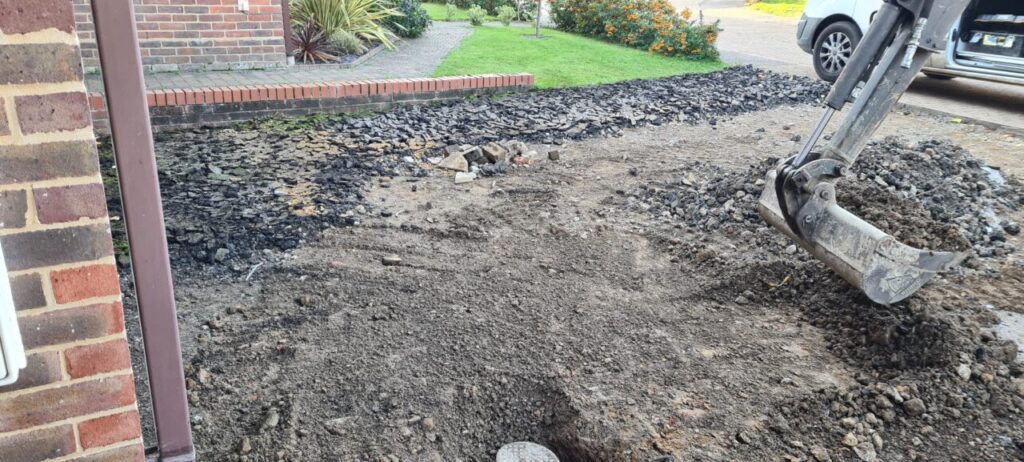
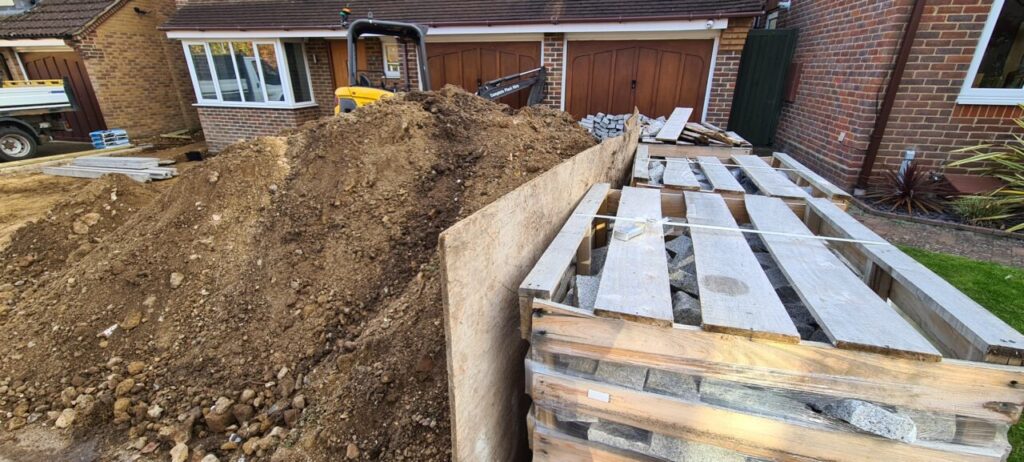
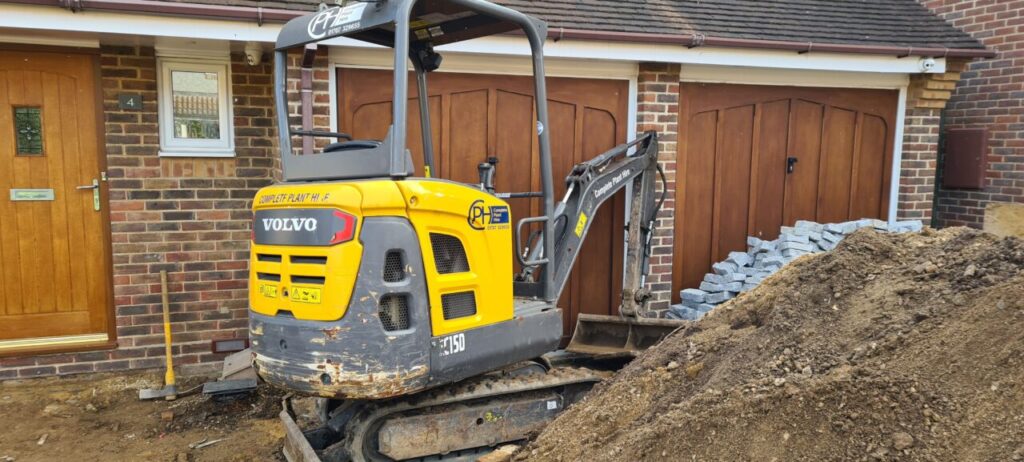
With half of the outdated tarmac drive clear the subsequent job was break up the outdated tarmac driveway. With two of us on Jackhammers this took us simply over in the future. The tarmac that was not stuffed with mud and moss was put to at least one aspect in a pile able to be combined with the MoT kind 1 as a part of the subbase to be unfold throughout the positioning. This did contain shifting the cobbles once more to realize entry to the final a part of the outdated drive.
At this level we had a big pile of spoil in the course of the positioning so we organised a Muck Away service to carry a seize lorry and scoop up the spoil and take it away. This left us with simply the pile of cobblestones able to be laid and a pile of tarmac chippings which might be used as crush to combine in with the MoT Kind 1.
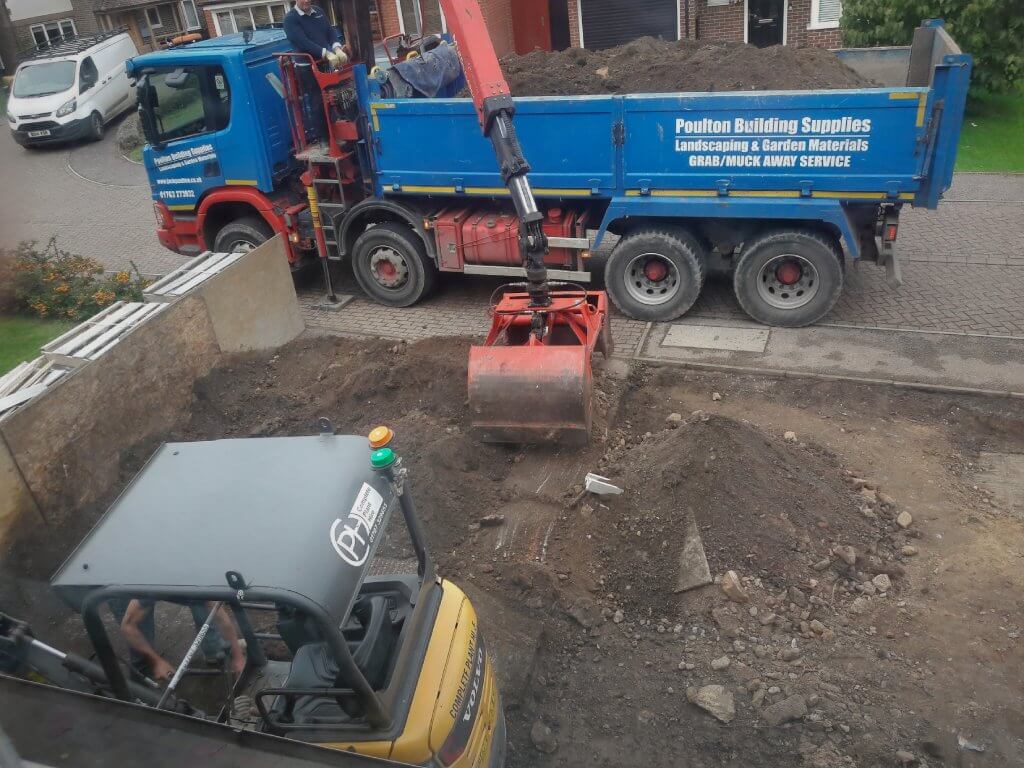
Posts and Panels
Up up to now within the venture all of the work had been at floor degree however now we wanted to erect a six foot closeboard fence half means up the drive after which a 600mm gray composite slatted fence to the tip of the drive. A part of the neighbours outdated concrete drive was damaged as much as accommodate the fence posts which had been cemented in utilizing quick setting postcrete after which the panels had been slid into place.
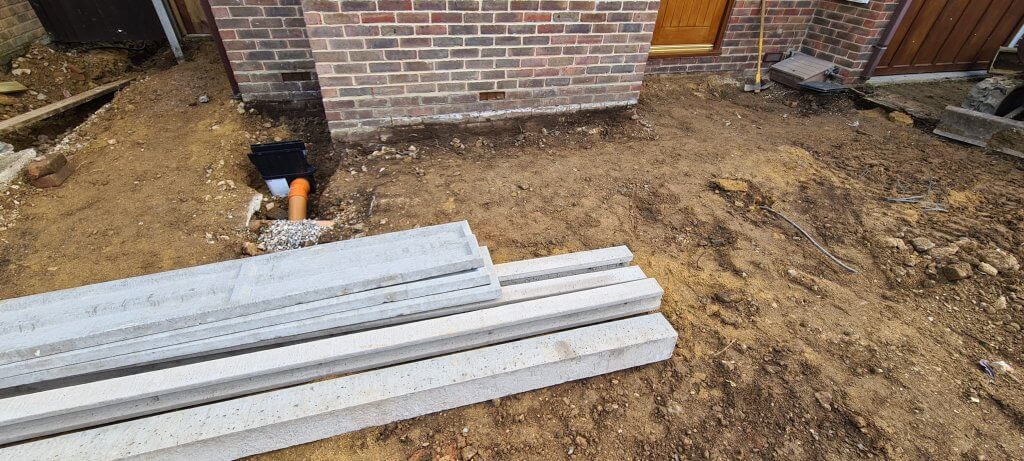
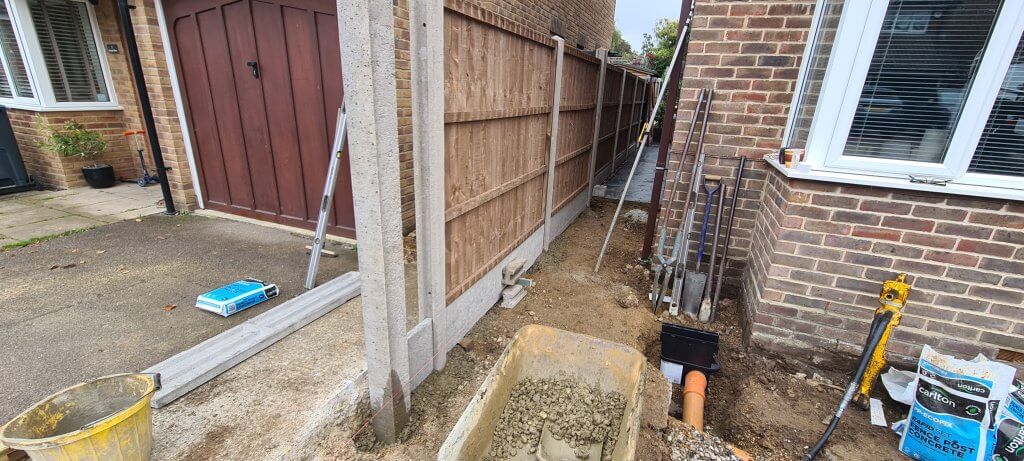
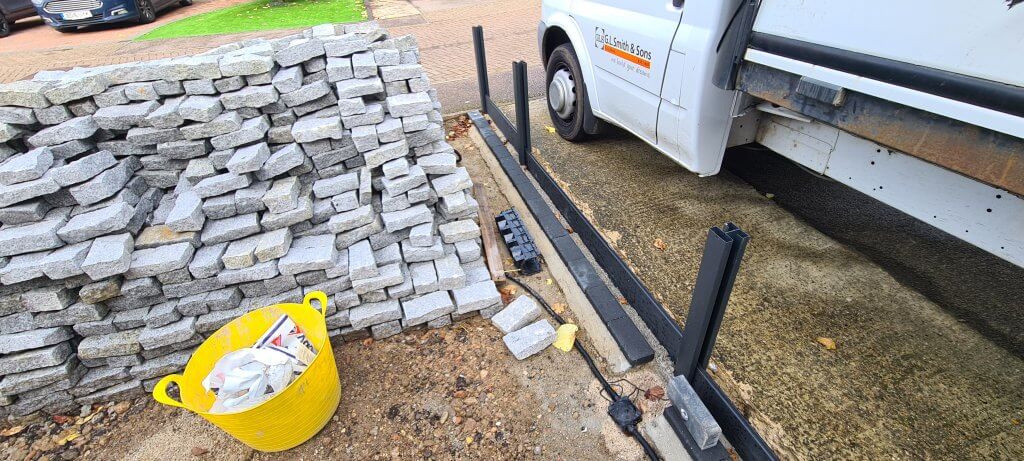
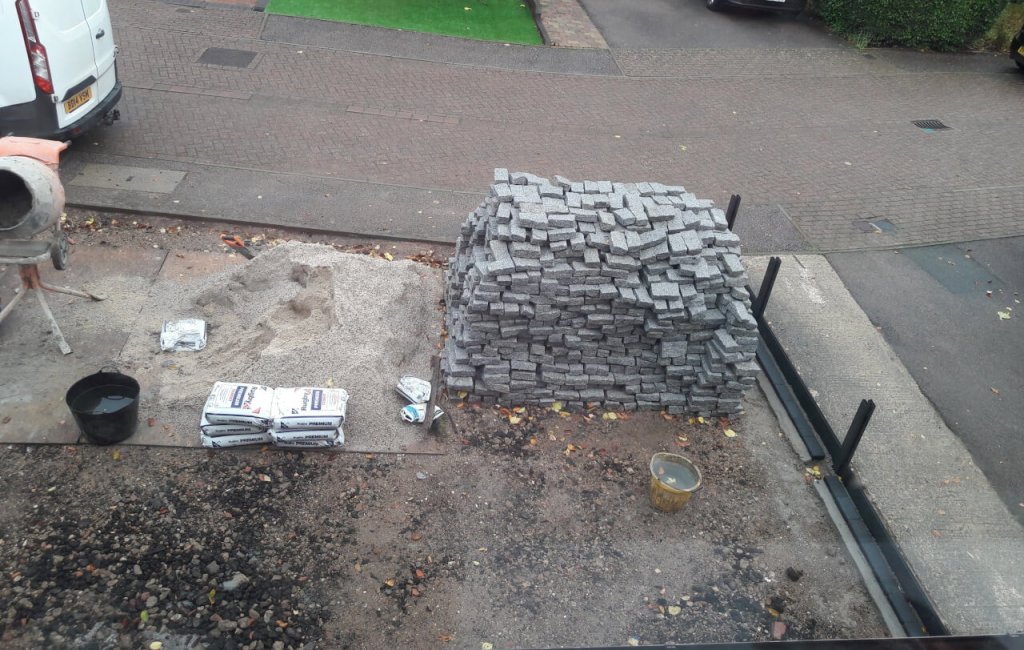
Chambers and Channel Drains
Simply exterior the entrance door and proper within the path proposed for the channel drain lay an inspection chamber that serviced the downstairs WC. It had been put in with a plastic cowl and glued in place at a jaunty angle so the one choice was to take away the present chamber and set up a brand new one the place the 110mm pipe went into the primary sewer line. The brand new chamber was put in with a versatile rubber connection connector and a 15 diploma bend. A riser was put in prepared to simply accept the 300mm block paver recessed body and tray.
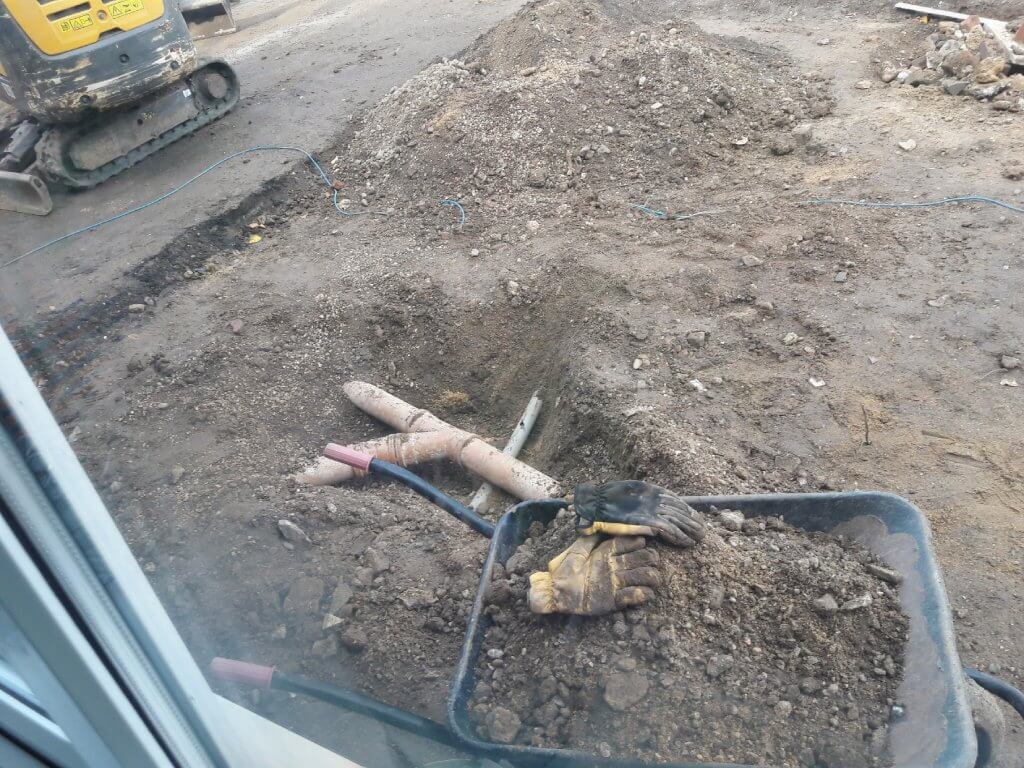
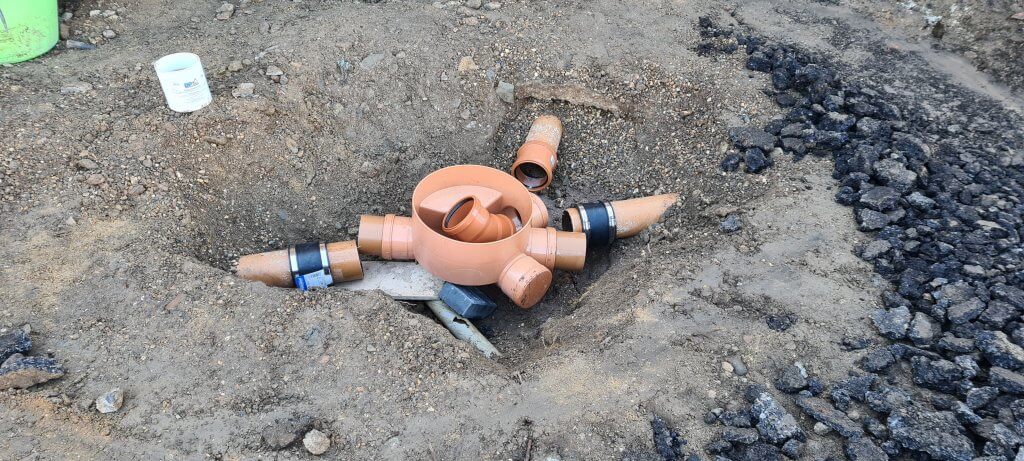
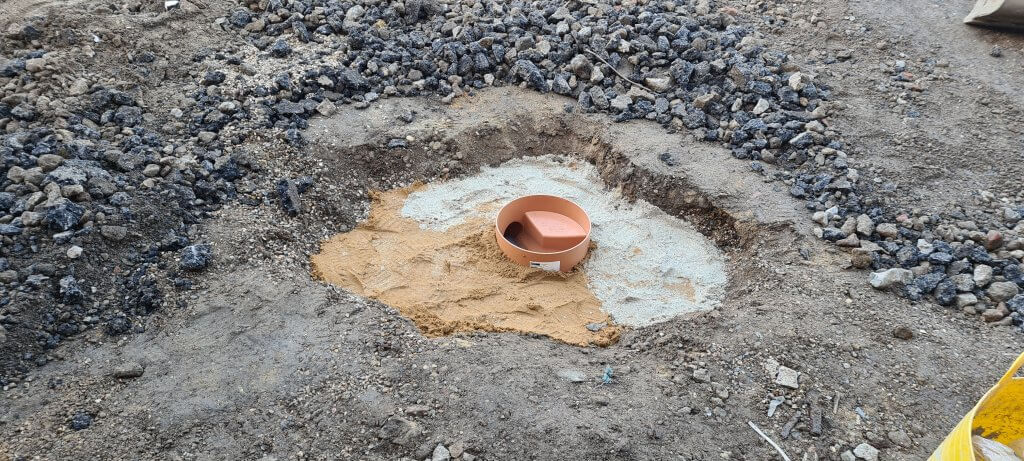
Additionally needing adjustment was the oval rodding eye entry cowl which required decreasing in order that much like the inspection chamber talked about earlier a 300mm block paver recessed body and tray may very well be put in above it.
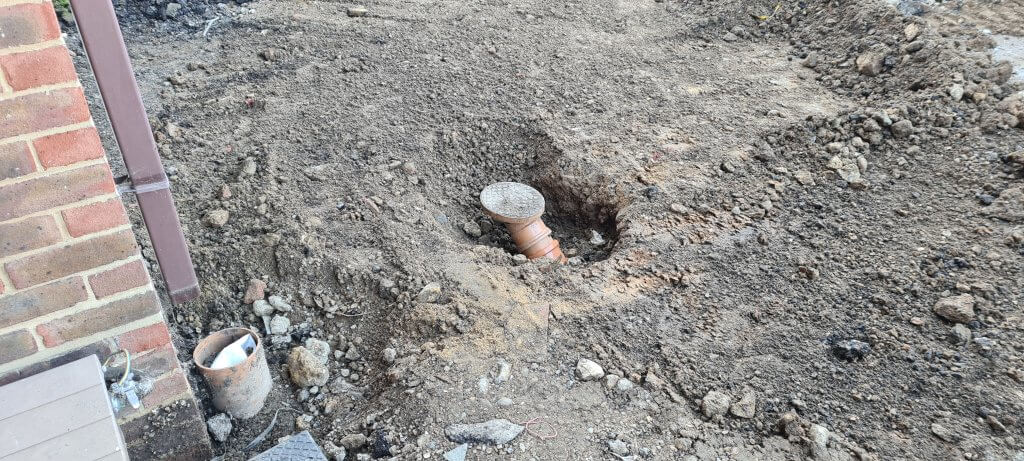
The subsequent job on the checklist was to put in the channel drains. A string line was run a protracted the trail of the channel drain on the appropriate peak and he channel drain our bodies had been clipped collectively and cemented in place. A gap was created within the channel drain to run into the present storm drain outlet for the left hand aspect of the drive and the sump for the correct hand aspect of the drive was related into the channel drain run as beforehand positioned.
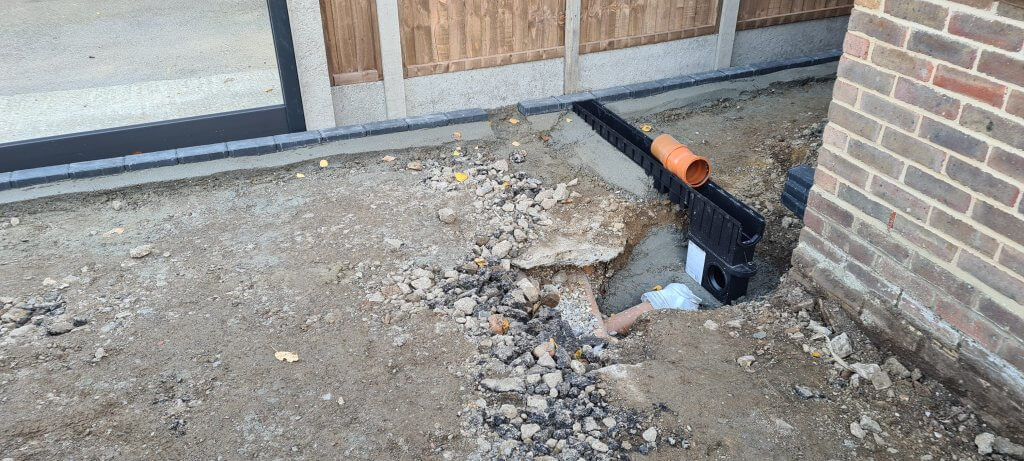
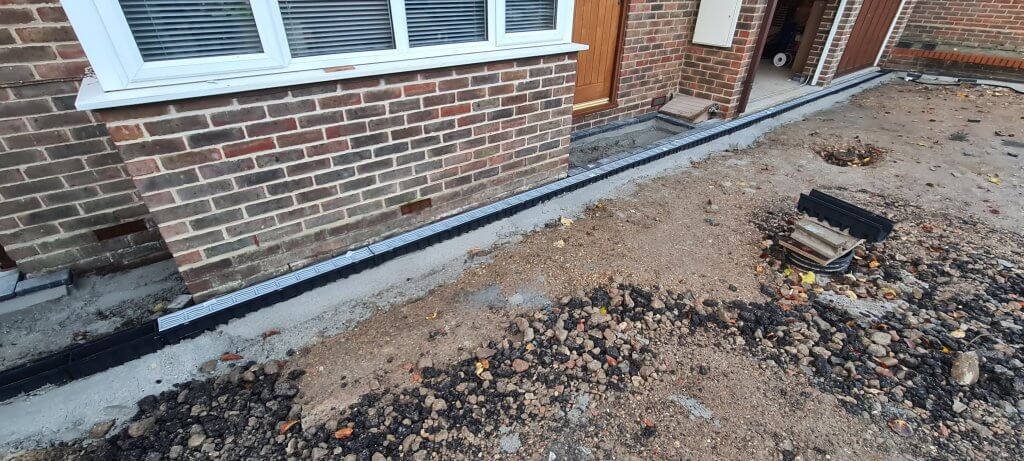
Drive Over Lights
Bordering your entire drive there was going to be a darkish gray engineered paviour that may even have the drive over lights set in it. So we drilled out 9 of the bricks to accommodate the lights with a diamond core bit and drill pouring loads of water over the drill bit to assist the grinding course of.
An armoured cable was run from a fused spurt within the storage to a weatherproof fused socket after which a brief extension lead was then run right into a climate proof socket field nonetheless contained in the storage. A plug was related to the LED mild driver which was housed in a junction field after which an exterior versatile cable was run from the drive into conduit. The conduit was run by means of a gap within the storage peer after which out onto the drive. Every mild had a Gel field and a Wiska field related to the conduit by a screw in conduit field connector with the sunshine related contained in the Gel field.
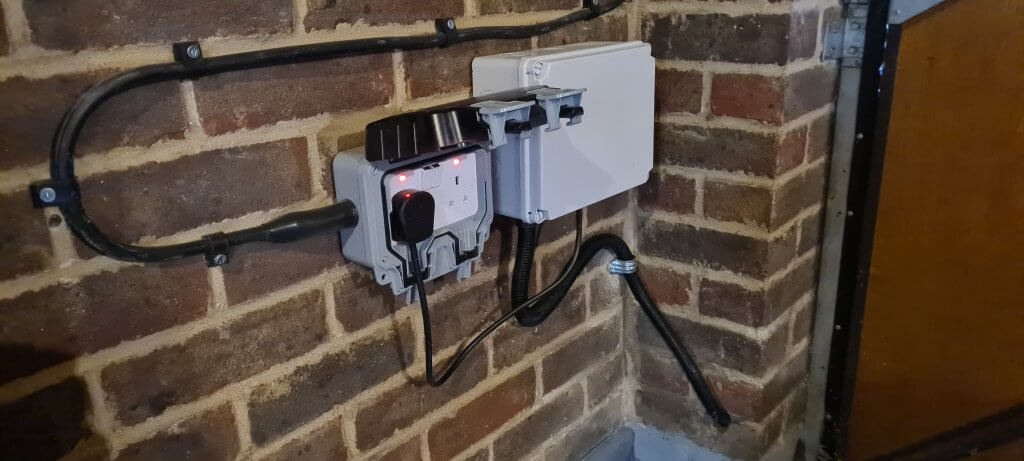
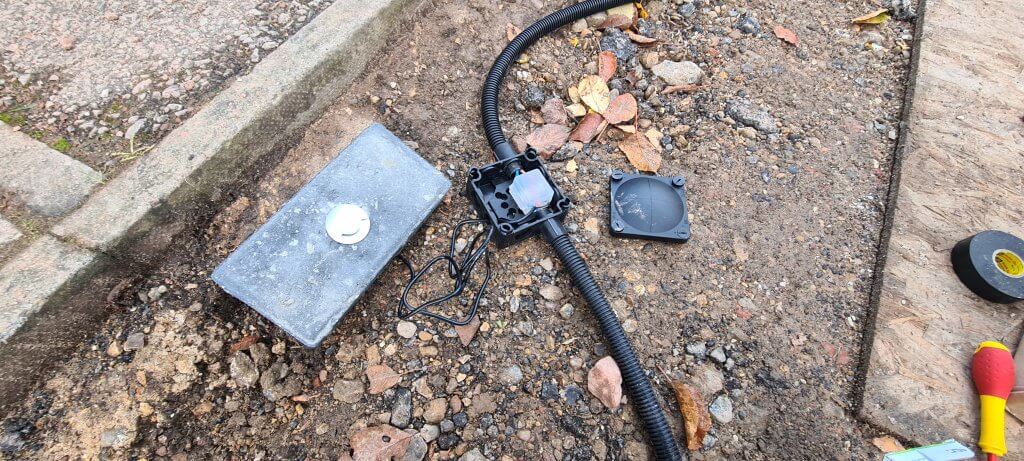
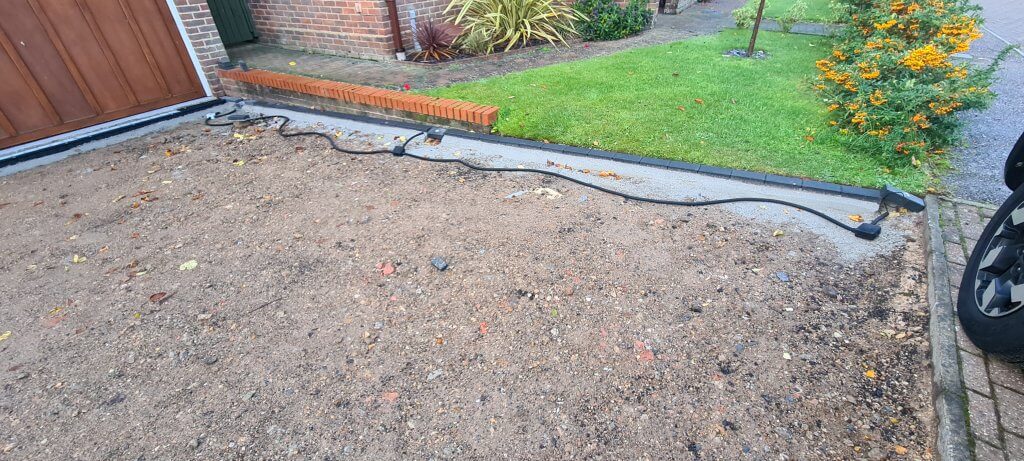
The Wiska field and conduit are buried underneath the sort 1 with the flex from the drive over mild being tucked underneath the engineered brick as soon as inserted to permit the sunshine to be modified if it ought to fail sooner or later.
Paviours and Granite Cobble Setts
Now the lighting gear has been put in it’s time to prepare to put the engineered bricks that body the cobbles and the cobble setts themselves however first a layer of MoT kind 1 and the damaged up tarmac wanted to be unfold throughout the positioning after which compacted down with the Compactor Plate. A string line was pulled throughout the positioning to offer a degree for the crush that may enable for 50mm of cement after which the 30 to 70mm for the cobbles which themselves fluctuate a good quantity in depth. By shifting the crush round and utilizing the whacker plate the required degree was achieved prepared for the bricks to be laid.
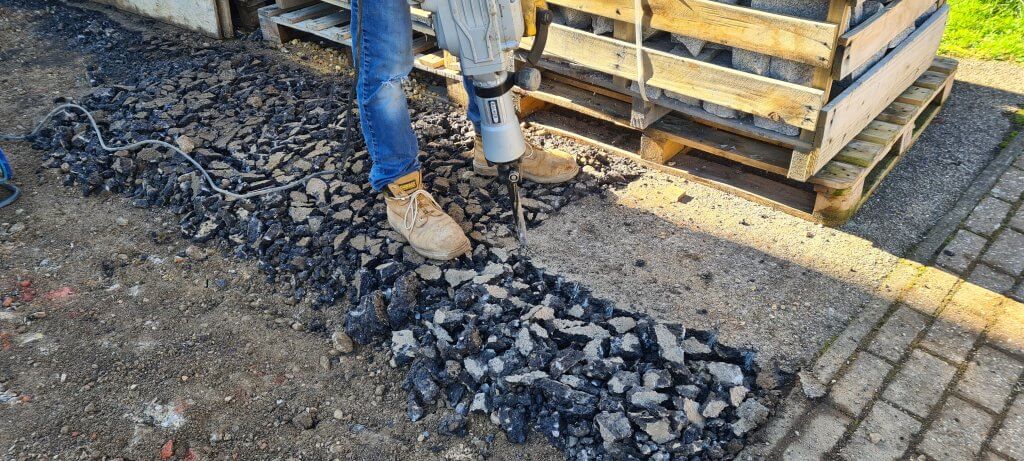
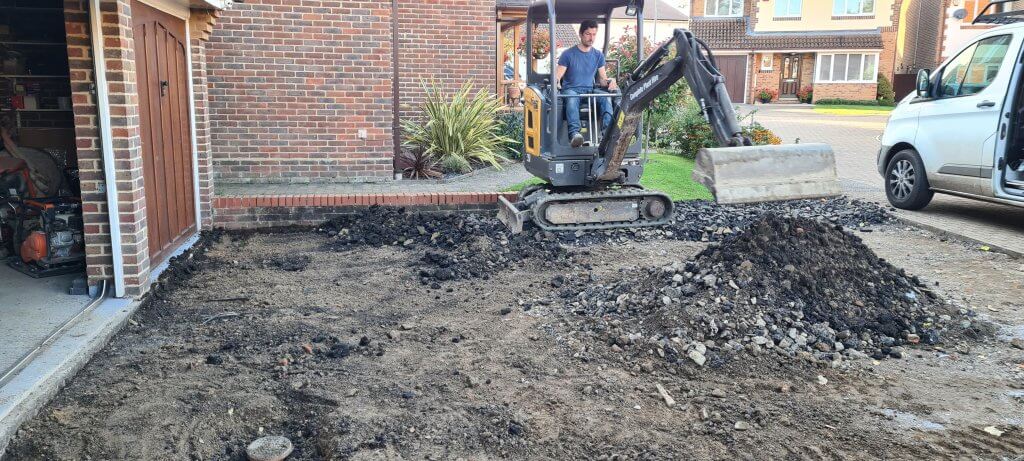
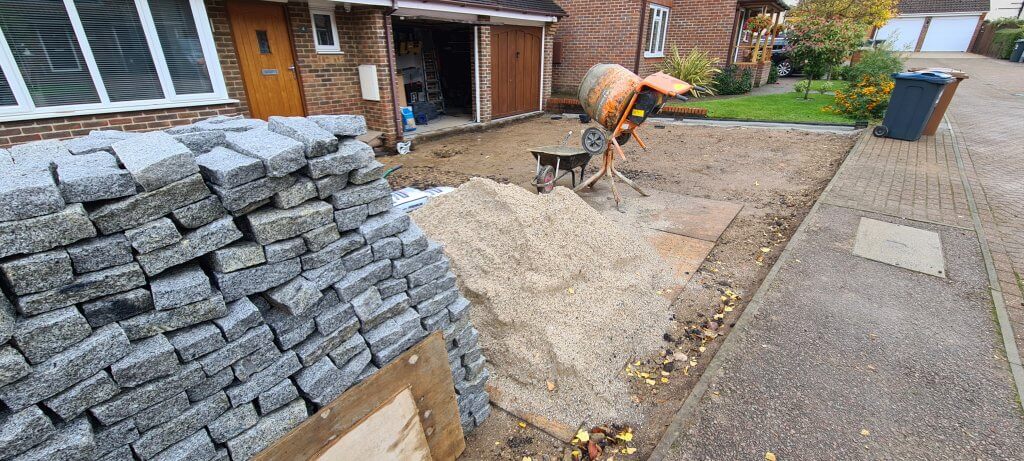
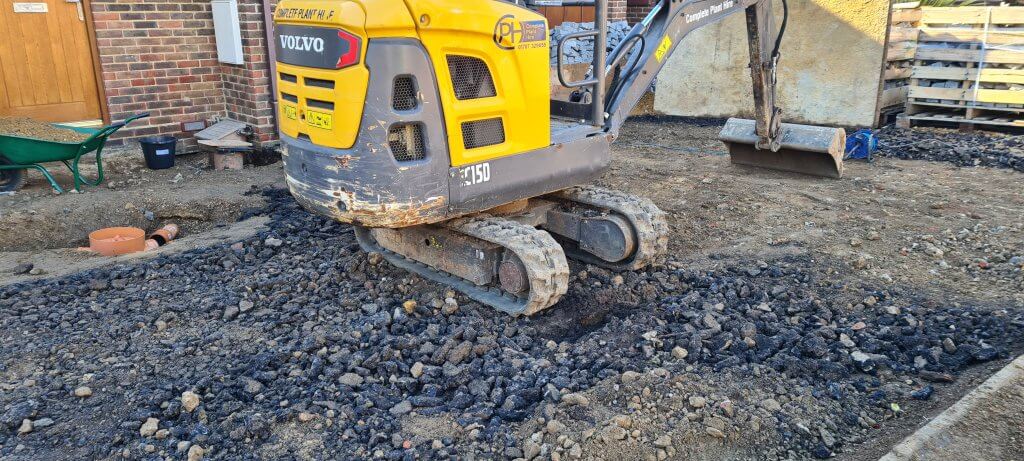
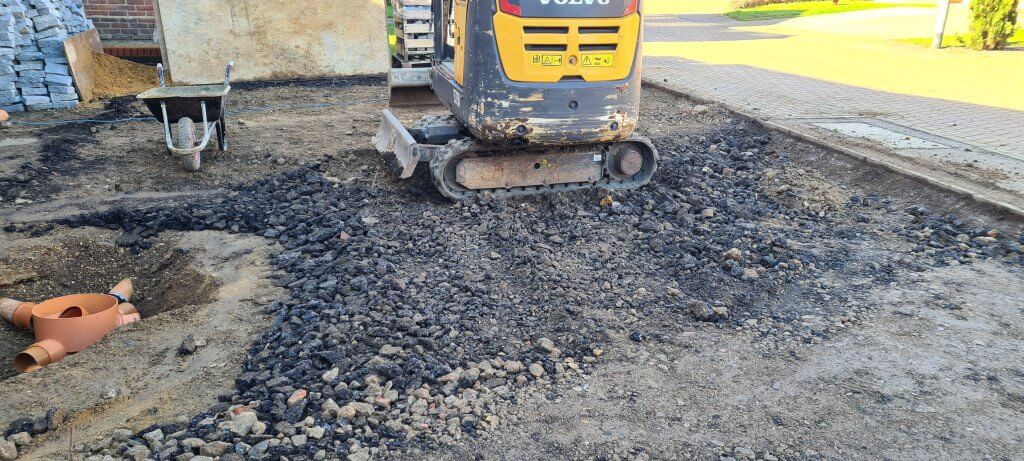
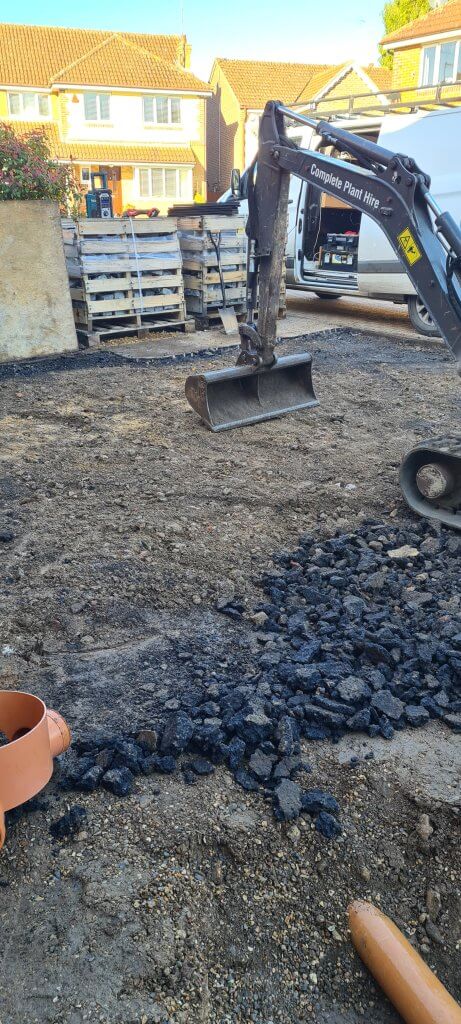
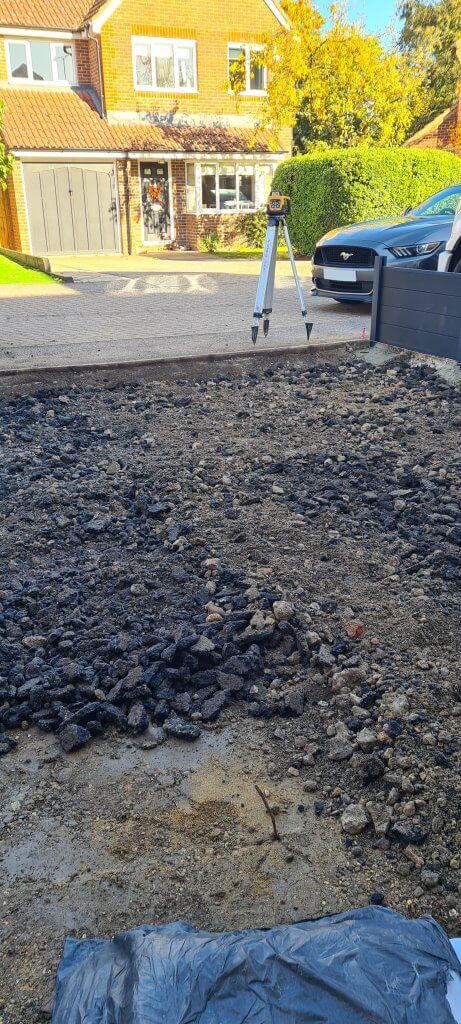
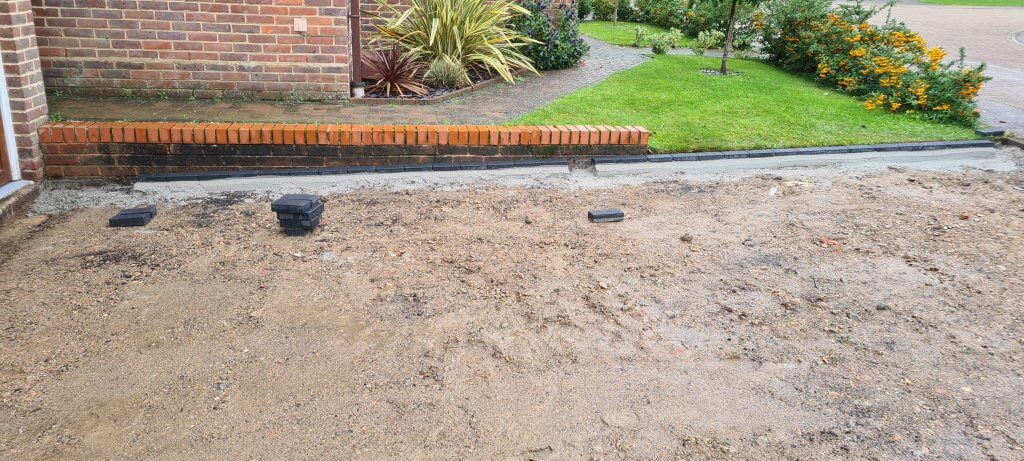
Then the engineered gray edging bricks had been laid. This outlined the place the highest of the drive floor was going to be. Each the engineered edging bricks and granite cobbles are being laid on a pointy sand and cement combine that’s pretty stiff in consistency, not too moist. The bricks a tapped down with a rubber mallet to offer the specified degree. The cobbles being pretty uneven in form signifies that knocking them into place is just not a exact science however a case of constructing the excessive spots all degree with one another.
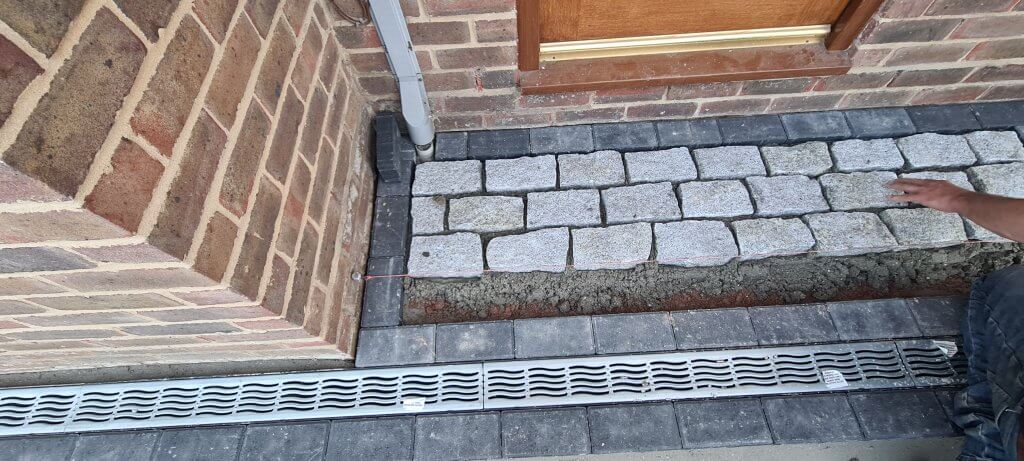
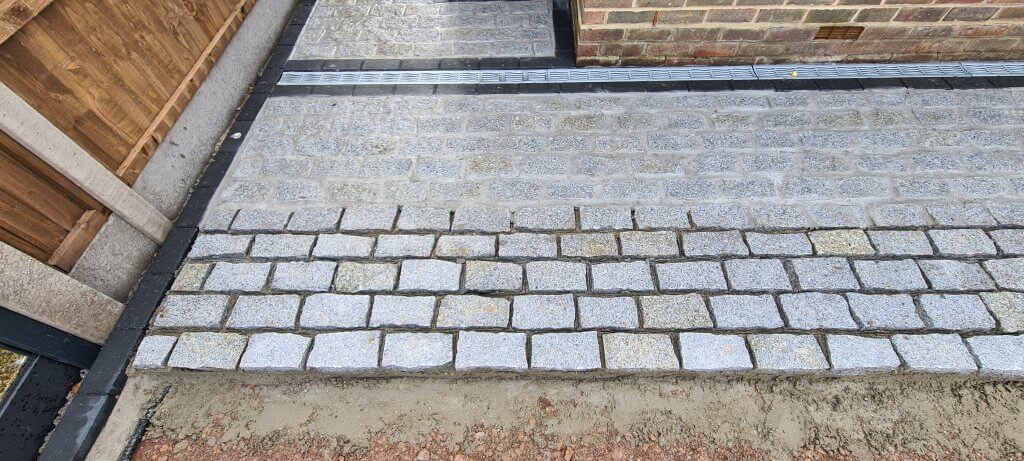
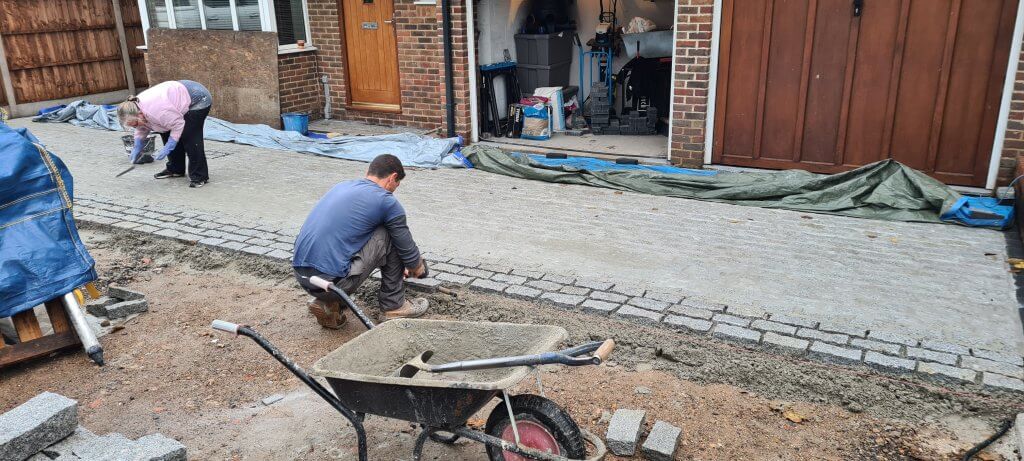
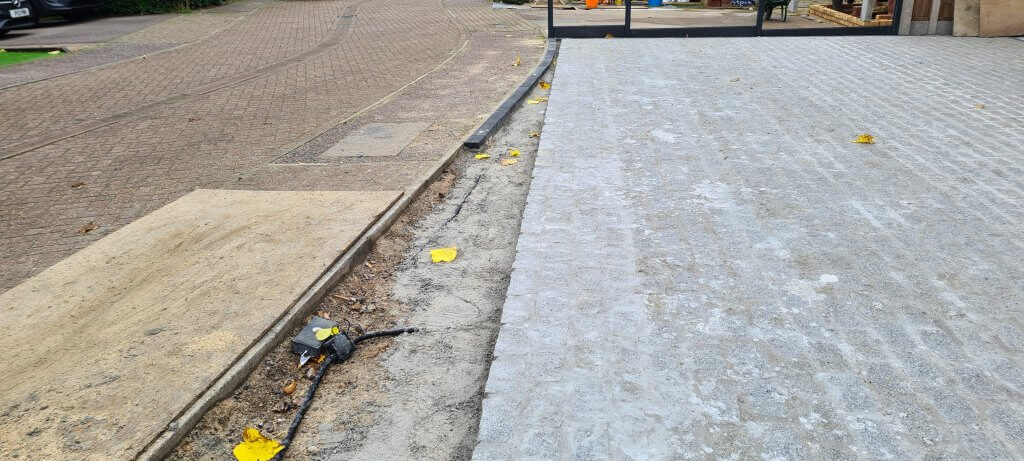
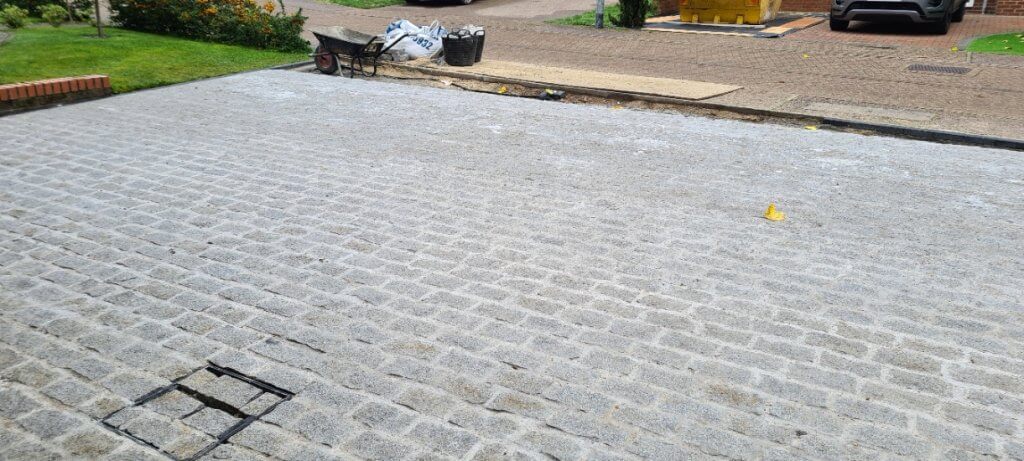
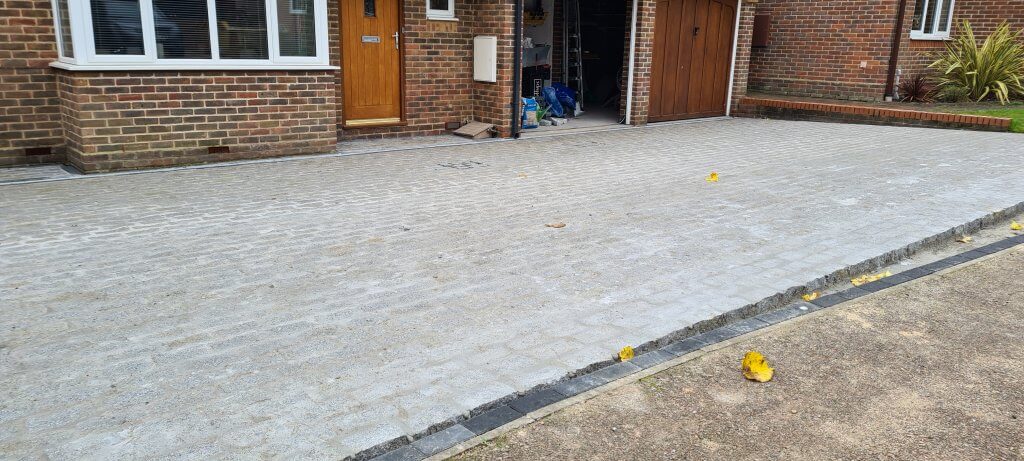
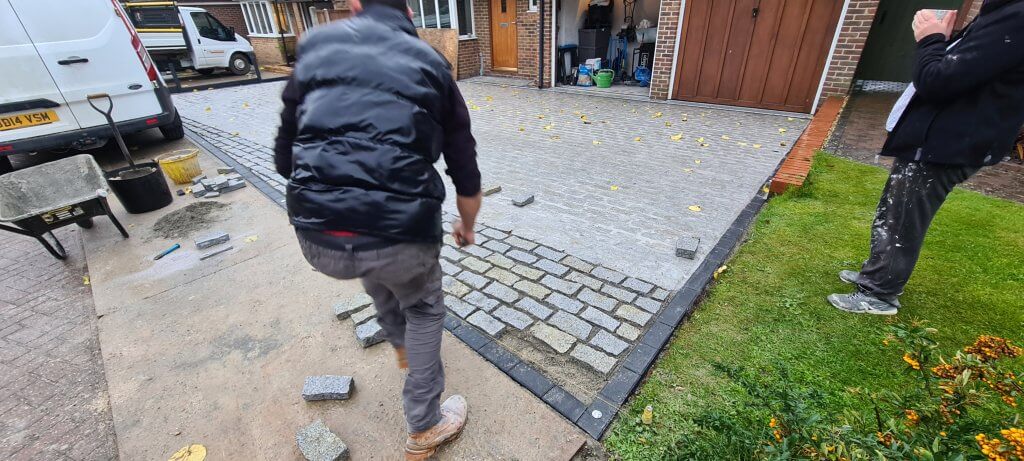
An angle grinder was used to chop the granite for the half bricks on the finish of the rows with the help of a pressurised water bottle with foot pump and 3m hose for mud suppression. A manhole body cowl was used to go over the now sunken chamber and rodding eye enabling cobbles to be inset into the body cowl.
Gunning within the Gunnable Pointing Mortar
A gunnable pointing mortar was chosen for its structural properties because it dries very arduous giving the cobbles a really sturdy development. We combined up one 25kg bag at a time with a mixing paddle in a trug bucket. As soon as combined we trowled the mortar into the mortar gun utilizing a cutdown funnel. We let the mortar go off for half an hour earlier than placing the mortar joints after which leaving it once more one other half hour or so earlier than washing off the surplus with a sponge. The ultimate stage was to wipe the cobbles clear. The method may be very labour intensive and time consuming however is a reasonably clear means of getting the grout effectively into the gaps of the sharp uneven joint faces that make up the granite cobble setts.
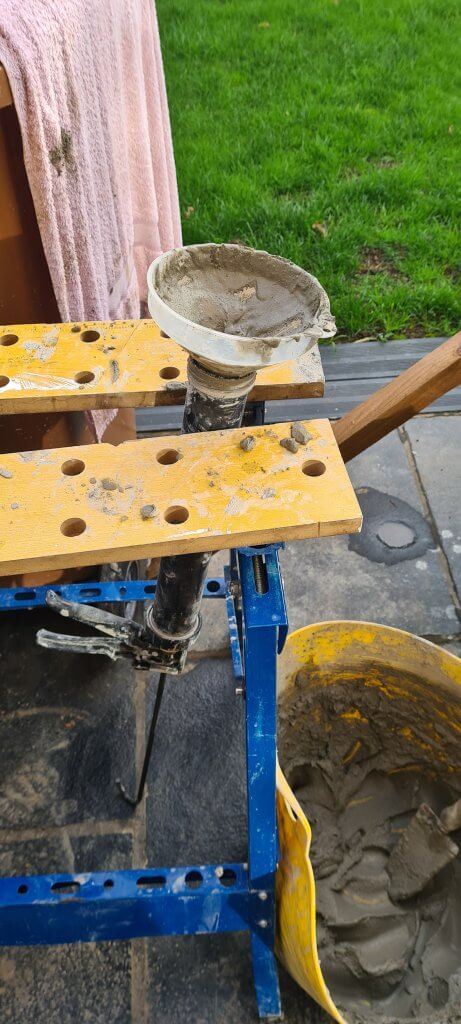
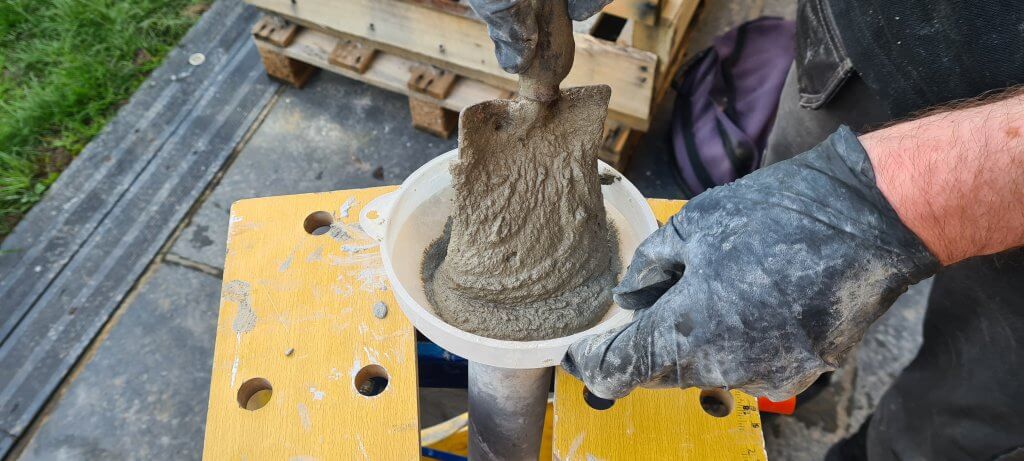
The final job was to fill the hole between the channel drain and the step into the storage with the gunnable mortar feathering it into the slope of the present concrete storage flooring.
It has taken 5 weeks to rework a disintegrating drive and overgrown entrance garden right into a model new cobbled driveway enhanced with drive over lights and black edging stones. The final job will entails cleansing the grout haze from the cobbles as soon as we get a number of dry days after which lastly inserting a few tall planters on the sting to melt the impact.
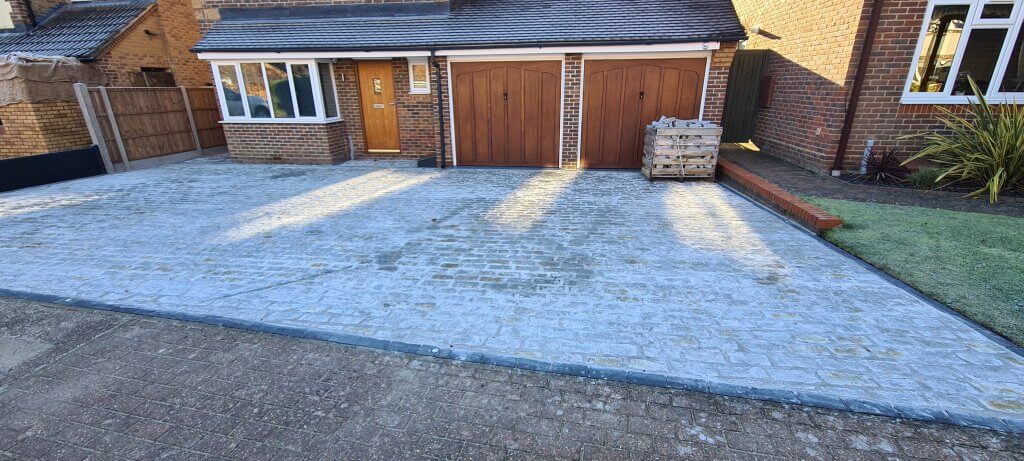
[ad_2]